Electrical Cable Cleat Types and Installation: A Comprehensive Guide
- Nasco Corp
- Jun 30
- 5 min read
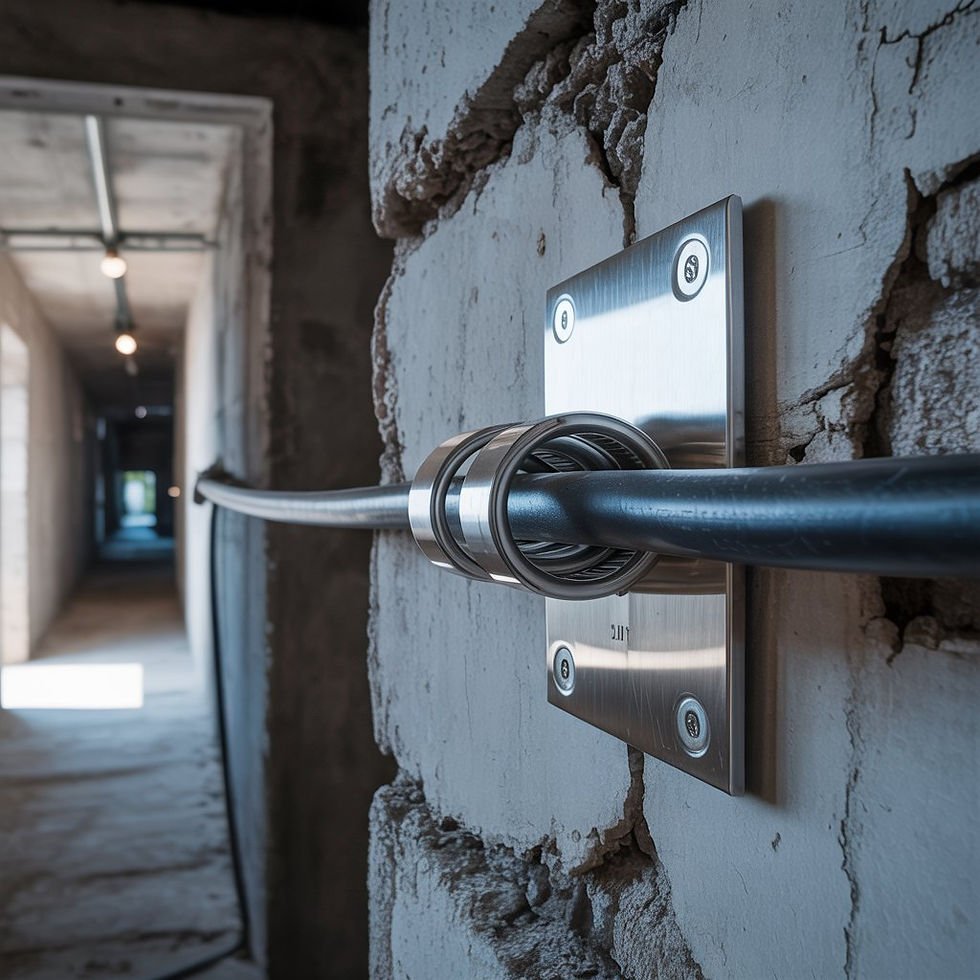
What are the types of electrical cable cleats, and how are they installed? Electrical cable cleats are devices used to secure and support electrical cables, ensuring safety and organization in various settings. They come in types like single, trefoil, and quad cleats, each suited for specific cable configurations and environments. Installation involves selecting the right cleat, using appropriate tools, and following best practices for secure mounting, especially on cable trays or in high-voltage systems.
This article explores cable cleat types, their applications, and step-by-step installation guidelines, optimized for clarity and expertise to help electricians, engineers, and facility managers ensure safe and efficient cable management.
What Are Cable Cleats?
Cable cleats are mechanical devices designed to fix, retain, and support electrical cables, preventing movement due to weight, external forces, or short-circuit stresses. They are critical for maintaining cable integrity, ensuring safety, and complying with electrical standards like IEC 61914.
Key Functions of Cable Cleats
Secure Cables: Prevent movement or damage during operation or faults.
Ensure Safety: Reduce risks of electrical faults or fire hazards.
Organize Systems: Maintain neat cable arrangements for maintenance and scalability.
Protect Against Stress: Absorb mechanical stresses in high-voltage or dynamic environments.
Types of Electrical Cable Cleats
Cable cleats vary based on cable type, configuration, and installation environment. Below are the primary types:
1. Single Cable Cleats
Purpose: Designed for securing individual cables.
Applications: Used in low-voltage systems or single-phase installations.
Materials: Available in plastic, aluminum, or stainless steel for corrosion resistance.
Example: Ideal for residential wiring or small-scale industrial setups.
2. Trefoil Cable Cleats
Purpose: Hold three cables in a triangular (trefoil) formation, common in three-phase systems.
Applications: Widely used in high-voltage installations to manage short-circuit forces.
Materials: Typically stainless steel or reinforced polymers for durability.
Example: Found in power plants or large industrial facilities.
3. Quad Cable Cleats
Purpose: Secure four cables, often in high-density setups.
Applications: Used in complex systems requiring multiple cables, like data centers.
Materials: Heavy-duty metals for high mechanical strength.
Example: Common in large-scale renewable energy projects.
4. Cable Cleats for Cable Trays
Purpose: Specifically designed for mounting on cable trays, ensuring organized cable routing.
Applications: Industrial settings, commercial buildings, or infrastructure projects.
Features: Adjustable designs to accommodate various tray sizes and cable diameters.
5. Specialty Cleats
Fire-Resistant Cleats: For environments requiring fire safety compliance.
Low-Smoke Zero-Halogen (LSZH) Cleats: Used in confined spaces like tunnels.
High-Voltage Cleats: Engineered for high-voltage cables to withstand extreme forces.
Cable Cleat Installation: Step-by-Step Guide
Proper cable cleat installation ensures safety, longevity, and compliance with standards. Below is a structured guide for installing cable cleats, including best practices for cable trays and high-voltage systems.
Tools for Electrical Cable Cleat Installation
Torque Wrench: Ensures precise tightening of bolts.
Cable Cutters: For trimming cables to fit cleats.
Measuring Tape: To space cleats accurately.
Drill and Bits: For mounting cleats on trays or walls.
Insulation Tester: To verify cable integrity post-installation.
Read This Also...Tools for Electrical Cable Cleat Installation
Steps for Cable Cleat Installation
Select the Right Cleat:
Match cleat type to cable size, configuration, and environment (e.g., trefoil for three-phase cables).
Check material compatibility (e.g., stainless steel for corrosive environments).
Plan the Layout:
Measure cable runs and mark cleat positions, typically every 0.3–1.2 meters, per IEC 61914.
Ensure cleats align with cable tray supports or mounting surfaces.
Prepare the Surface:
Clean cable trays or mounting surfaces to remove debris.
Verify structural integrity of the mounting area.
Install Cleats:
Secure cleats using bolts or screws, applying torque as per manufacturer specifications.
For cable trays, use tray-specific cleats with compatible brackets.
Position Cables:
Place cables in cleats, ensuring no undue stress or bending.
For high-voltage cables, confirm cleats can withstand short-circuit forces.
Tighten and Test:
Tighten cleats to secure cables without crushing insulation.
Use an insulation tester to confirm no damage occurred during installation.
Inspect and Document:
Verify alignment, spacing, and torque.
Document installation details for compliance and future maintenance.
Best Practices for Cable Cleat Installation
Follow Standards: Adhere to IEC 61914 or local electrical codes.
Space Cleats Correctly: Ensure even spacing to prevent cable sagging or strain.
Use Quality Materials: Choose cleats resistant to environmental factors like UV or corrosion.
Avoid Over-Tightening: Prevent damage to cable insulation.
Test for Faults: Conduct post-installation tests to confirm system integrity.
Read This Also...Best Practices for Cable Cleat Installation
Cable Cleat Installation in Industrial Settings
Industrial environments, such as power plants or manufacturing facilities, demand robust cable management due to high-voltage systems, heavy machinery, and harsh conditions. Key considerations include:
High-Voltage Cable Cleats: Use heavy-duty cleats designed for short-circuit forces, typically made of stainless steel or reinforced composites.
Cable Trays in Industrial Setups: Ensure cleats are compatible with tray designs and can handle dynamic loads.
Environmental Factors: Select cleats with corrosion resistance for outdoor or chemical-heavy environments.
Real-Life Example: In a 2023 solar farm project, trefoil cleats were used to secure high-voltage cables on cable trays, reducing installation time by 20% due to pre-planned spacing and modular cleat designs. Read This Also...Cable Cleat Installation in Industrial Settings
Optimizing Cable Cleat Installation for High-Voltage Cables
High-voltage cables require specialized cleats to manage electromagnetic forces and thermal expansion. Best practices include:
Cleat Strength: Choose cleats rated for short-circuit forces (e.g., 100 kA for 1 second).
Material Selection: Use stainless steel or fire-resistant materials for safety.
Spacing: Follow manufacturer guidelines, typically closer spacing (0.3–0.6 meters) for high-voltage systems.
Example: In a 2024 wind farm installation, quad cleats were used to secure high-voltage cables, ensuring stability during peak load conditions. Read This Also...Cable Cleat Installation for High Voltage Cables
FAQs About Cable Cleat Types and Installation
Q: What is the purpose of cable cleats?
A: Cable cleats secure and support electrical cables, preventing movement, ensuring safety, and maintaining system integrity during faults.
Q: How often should cable cleats be installed along a cable run?
A: Cleats are typically spaced every 0.3–1.2 meters, depending on cable type, configuration, and standards like IEC 61914.
Q: Can cable cleats be used on all types of cables?
A: Yes, but the cleat type must match the cable configuration (e.g., single, trefoil) and environment (e.g., high-voltage, fire-resistant).
Q: What tools are essential for cable cleat installation?
A: Essential tools include a torque wrench, cable cutters, measuring tape, drill, and insulation tester.
Q: Are there special considerations for high-voltage cable cleat installation?
A: High-voltage installations require cleats rated for short-circuit forces, closer spacing, and materials like stainless steel for durability.
Conclusion
Cable cleats are vital for safe and efficient electrical systems, with types like single, trefoil, and quad cleats serving specific purposes. Proper installation, especially on cable trays or in industrial and high-voltage settings, requires careful planning, quality tools, and adherence to best practices. By following standards and using the right cleats, you can ensure long-lasting, safe cable management.
Comments